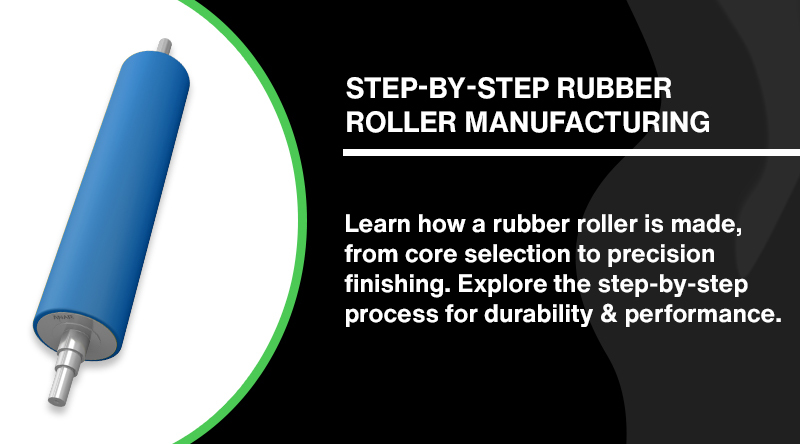
A rubber roller is a key component in printing, packaging, textiles, and steel processing industries. It ensures smooth material handling and durability in various operations. But have you ever wondered how these rollers are made?
This guide will take you through the step-by-step manufacturing process, showing how precision and quality materials create a long-lasting product. 📌 Looking for industrial rollers? Explore our rubber roller solutions at Anar Rub Tech.
Step 1: Selecting the Right Core Material
The core material determines the strength and durability of the roller.
Common Core Materials:
Steel: Ideal for heavy-duty applications.
Aluminum: Lightweight and corrosion-resistant.
Composite Materials: Used where weight reduction is important.
Step 2: Surface Preparation for Strong Adhesion
Before coating, the core must be treated for better bonding.
✅ Cleaning to remove oil and contaminants.
✅ Surface roughening to improve adhesion.
✅ Applying a bonding agent for a secure grip.
Step 3: Choosing the Right Rubber Compound
The outer layer is selected based on industry requirements.
🔹 Natural Rubber: High elasticity and abrasion resistance.
🔹 Nitrile (NBR): Oil and chemical resistance.
🔹 Silicone: Withstands high temperatures.
🔹 EPDM: Suitable for outdoor conditions.
Step 4: Rubber Application & Layering
The rubber is applied using precise techniques:
✔ Extrusion for uniform coating.
✔ Calendaring for even thickness.
✔ Molding for custom designs.
Step 5: Curing & Vulcanization for Strength
The roller undergoes heat treatment to enhance durability.
✅ Increases wear resistance and flexibility.
✅ Protects against extreme temperatures.
✅ Prevents premature breakdown.
Step 6: Precision Grinding & Surface Finishing
After curing, the roller is shaped for perfect fit and function.
🔹 Cylindrical grinding smooths the surface.
🔹 Grooving improves material grip.
🔹 Crowning balances pressure distribution.
Step 7: Quality Inspection & Final Testing
Strict tests ensure performance and reliability.
✅ Hardness testing checks material durability.
✅ Dynamic balancing prevents vibration.
✅ Surface inspection detects defects.
✅ Load testing simulates real use.
Conclusion
A rubber roller goes through several precision-driven steps to ensure strength and efficiency for industrial applications.
📌 Need high-performance rollers? Check out our rubber roller at Anar Rub Tech today!