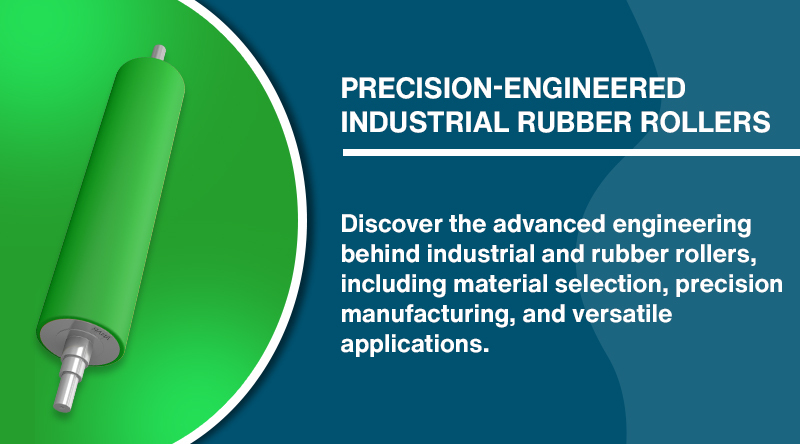
Industrial rollers, including rubber rollers, play a pivotal role in diverse applications across manufacturing, converting, and printing industries. These cylindrical components, such as rubber rollers, are designed for performance and durability and provide crucial functionality in processes like web handling, laminating, embossing, and material transportation. While their basic function might seem straightforward, the engineering behind these rollers involves a confluence of advanced materials, precision manufacturing, and tailored designs.
Material Composition and Selection
One of the most critical aspects of industrial rollers is the material composition of their outer coating. Commonly, these rollers are crafted using high-performance polymers, elastomers, or composites. The choice of material depends on the application, operating environment, and desired performance metrics. For instance:
Elastomers: These materials are often chosen for their elasticity, abrasion resistance, and ability to provide traction or grip. They are ideal for applications involving paper, textiles, or films where gentle handling is crucial.
Polyurethane Coatings: Known for their exceptional wear resistance and tensile strength, polyurethane-coated rollers excel in high-stress environments such as metal processing and heavy-duty conveyors.
Silicone Coatings: These are favored in industries requiring heat resistance and non-stick properties, such as food processing and plastic film production.
Manufacturing Precision
Modern manufacturing of industrial rollers involves precision engineering techniques to ensure concentricity, surface uniformity, and balance. These parameters are critical to avoid vibrations, uneven wear, or process inefficiencies. Key manufacturing steps include:
CNC Machining: Advanced CNC technology ensures that the roller core and outer layers are machined to tight tolerances. This process is vital for high-speed applications where even minor deviations can impact performance.
Dynamic Balancing: To prevent operational issues such as vibration or premature bearing wear, rollers undergo dynamic balancing. This involves calculating and adjusting weight distribution to achieve smooth rotation at operating speeds.
Surface Finishing: The surface texture of the roller is tailored to the application. Smooth finishes are typically used for laminating or printing, while textured surfaces are essential for gripping and feeding applications.
Key Performance Attributes
Industrial rollers are engineered with specific performance attributes to suit their intended use. Some of the critical performance factors include:
Load-Bearing Capacity: Rollers must be capable of withstanding the mechanical loads exerted during operation without deformation or fatigue.
Heat Resistance: Rollers are designed to maintain dimensional stability and surface integrity under high temperatures for applications like calendaring or hot pressing.
Chemical Resistance: In environments exposed to solvents, oils, or other chemicals, the outer coating material is selected to resist degradation and ensure longevity.
Abrasion Resistance: Rollers in high-friction scenarios, such as conveyor belts or material feeders, require coatings that can endure constant wear without compromising performance.
Applications Across Industries
The versatility of industrial rollers makes them indispensable in a range of industries, including:
Printing and Packaging: Used in flexographic printing, offset printing, and packaging machinery for precise ink transfer and material handling.
Textile and Paper Manufacturing: Essential for processes like dyeing, calendering, and web guiding to ensure uniformity and efficiency.
Metal Processing: Employed in rolling mills, sheet metal processing, and coil handling for precision and durability.
Food and Pharmaceutical Industries: Specialty coatings on rollers ensure compliance with hygiene standards while offering superior performance.
Maintenance and Longevity
Proper maintenance practices are vital to maximize the lifespan and performance of industrial rollers. Routine inspections for surface wear, concentricity, and bearing integrity can prevent downtime and costly replacements. Additionally, re-coating or refurbishing worn rollers, such as rubber rollers, is a cost-effective way to extend their service life while maintaining optimal performance.
Conclusion
Industrial rollers are highly engineered components that provide critical support in numerous industrial applications. Their performance is determined by material selection, manufacturing precision, and tailored designs. Understanding these technical details empowers businesses to choose the right rollers for their specific needs, ensuring enhanced efficiency, reliability, and productivity.